Maschinenstillstand ist teuer. Vor allem, wenn er ungeplant kommt. In der Industrie entscheiden oft Sekunden darüber, ob eine Linie weiterläuft – oder zum Stillstand kommt. Genau hier greift Predictive Maintenance ein: Statt auf starren Intervallen oder Reaktionen auf Defekte zu beruhen, überwacht diese Technologie den tatsächlichen Zustand von Maschinen – und prognostiziert Probleme, bevor sie eintreten. Echtzeitdaten, Sensorik und künstliche Intelligenz machen es möglich. Für Unternehmen ist das mehr als eine Spielerei: Es ist ein strategischer Hebel zur Kostensenkung, Effizienzsteigerung und Absicherung der Produktion.
Was genau hinter Predictive Maintenance steckt, wie die Systeme funktionieren und warum sich der Einstieg lohnt – dieser Artikel liefert die fundierten Antworten.
Was ist Predictive Maintenance?
Predictive Maintenance – auf Deutsch: vorausschauende Wartung – beschreibt einen Instandhaltungsansatz, bei dem Maschinen nicht nach Plan oder bei Ausfall gewartet werden, sondern genau dann, wenn ihre aktuellen Betriebsdaten es nahelegen. Grundlage sind Sensoren, die relevante Zustandsinformationen wie Temperatur, Vibration oder Stromaufnahme in Echtzeit erfassen. Diese Daten fließen in Algorithmen, die Muster erkennen, Abweichungen analysieren und frühzeitig vor Problemen warnen.
Das Ziel: Wartung nur dann, wenn sie wirklich notwendig ist – nicht zu spät, aber auch nicht zu früh. So lassen sich Stillstände vermeiden, Kosten senken und die Lebensdauer von Anlagen verlängern.
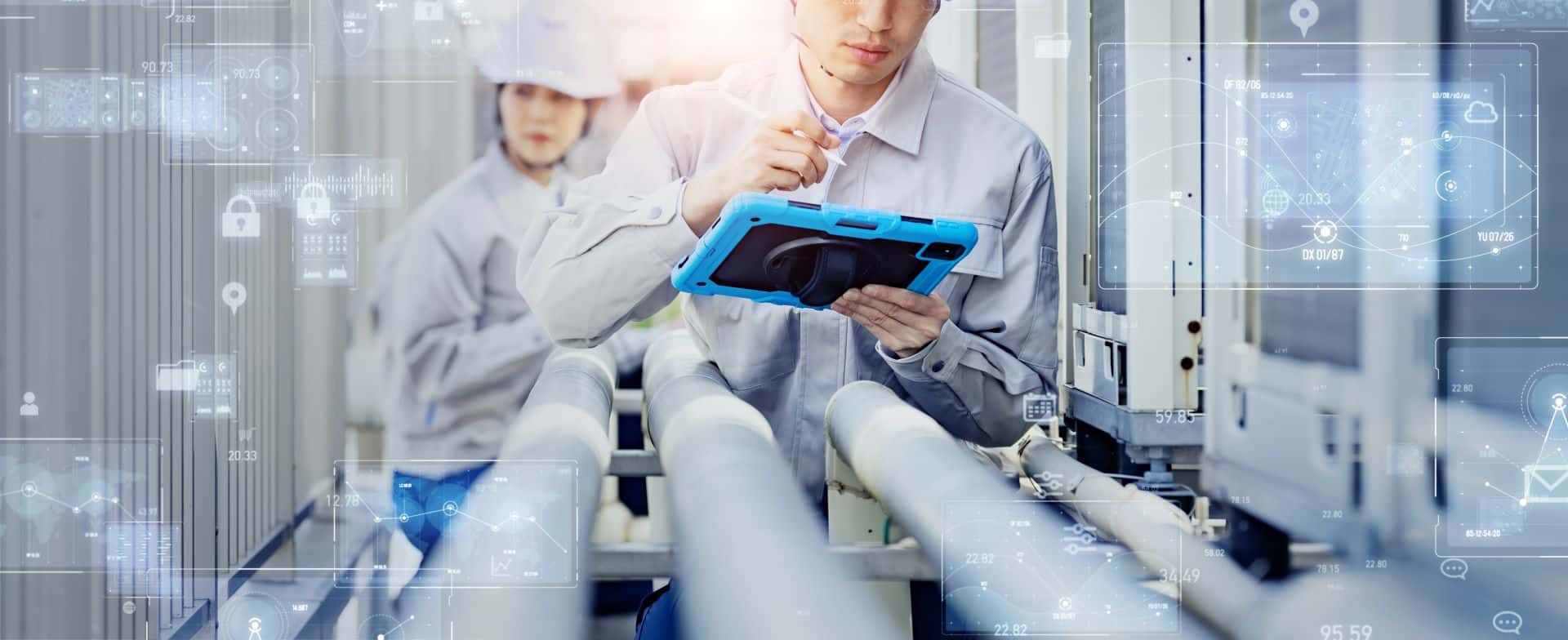
Der Unterschied zu herkömmlichen Wartungsarten
Wartungsart | Vorgehen | Risiko/Nachteil |
---|---|---|
Reaktive Wartung | Reparatur nach Ausfall | Ungeplante Stillstände, hohe Folgekosten |
Präventive Wartung | Wartung in festen Intervallen | Ressourcenverschwendung, unnötige Eingriffe |
Predictive Maintenance | Wartung bei konkreten Verschleißsignalen | Bedarfsgerechte Planung, minimale Ausfallrisiken |
Predictive Maintenance ist kein pauschales Rezept, sondern ein datengestützter Entscheidungsprozess. Wo bisher Erfahrungswerte oder starrer Zeitplan den Ton angaben, übernehmen heute Sensorik, KI und Systemtransparenz die Regie.
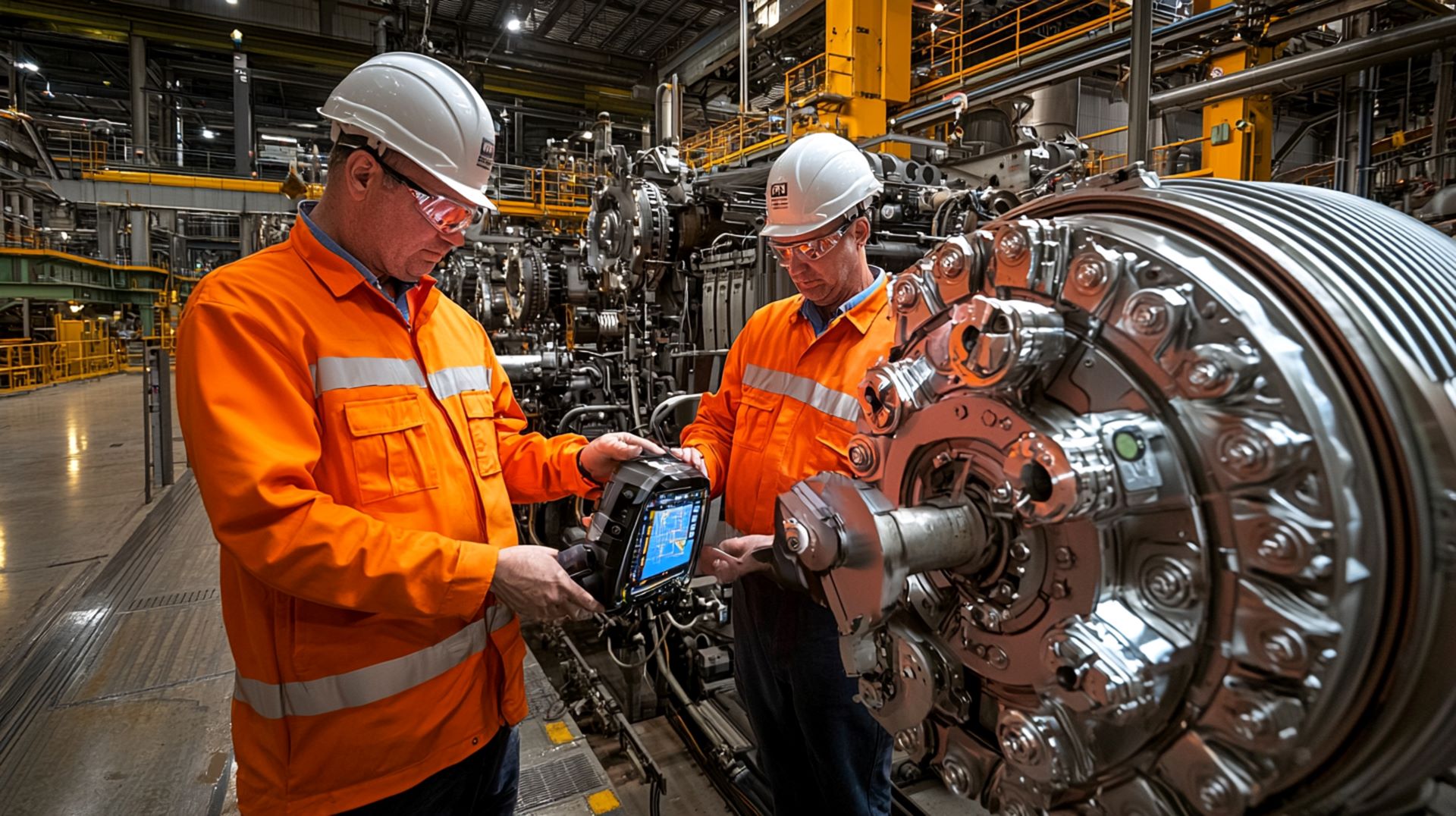
So funktioniert Predictive Maintenance
Die Grundidee ist simpel: Wer genug über den aktuellen Zustand einer Maschine weiß, kann drohende Probleme früh erkennen – und gezielt eingreifen. Möglich wird das durch ein Zusammenspiel aus Sensorik, Datenverarbeitung und intelligenter Prognose.
1. Sensorik: Die Sinne der Maschine
Zunächst wird die Maschine mit Sensoren ausgestattet. Diese erfassen kontinuierlich relevante physikalische Parameter:
-
Vibrationen – etwa bei Motoren, Lagern oder Pumpen
-
Temperatur – z. B. bei Reibung oder elektrischer Belastung
-
Druck – in Hydraulik- oder Pneumatiksystemen
-
Stromverbrauch – zur Erkennung von Effizienzverlusten
-
Akustische Signale – für feinste Abweichungen im Betrieb
2. Datenerfassung und Vorverarbeitung
Die gesammelten Daten landen entweder direkt in der Cloud oder werden per Edge Computing lokal verarbeitet. Wichtig: Bereits hier erfolgen Filterung und erste Analysen, um Ausreißer zu erkennen oder Signale zu glätten.
3. Analyse und Mustererkennung
Anschließend kommen Algorithmen zum Einsatz – meist aus dem Bereich Machine Learning. Sie erkennen Anomalien, vergleichen aktuelle Werte mit historischen Mustern und berechnen den Remaining Useful Life (RUL), also die verbleibende Nutzungsdauer eines Bauteils.
Je mehr Daten das System kennt, desto genauer wird die Vorhersage. Überwachung wird so zur Voraussage – und Wartung zur kalkulierten Maßnahme.
4. Handlungsempfehlung in Echtzeit
Bei Auffälligkeiten sendet das System automatisch eine Benachrichtigung: „Lager XYZ zeigt erhöhtes Schwingungsverhalten – Austausch empfohlen innerhalb der nächsten 5 Tage.“ Manche Lösungen integrieren direkt die Ersatzteilverfügbarkeit oder schlagen freie Wartungsfenster vor.
Das spart nicht nur Zeit, sondern verhindert kostspielige Pannen – bevor sie entstehen.
Vorteile der Predictive Maintenance
Wer Predictive Maintenance einsetzt, optimiert nicht nur die Technik – sondern das gesamte Betriebsmodell. Die Vorteile reichen von konkreten Kosteneinsparungen bis hin zu strategischem Wettbewerbsvorteil.
1. Geringere Ausfallzeiten
Ungeplante Stillstände zählen zu den größten Kostenfaktoren in der Industrie. Predictive Maintenance reduziert das Risiko technischer Ausfälle erheblich. Probleme werden erkannt, bevor sie zu Störungen führen.
2. Verlängerte Lebensdauer der Maschinen
Regelmäßige, aber gezielte Wartung schützt vor Folgeschäden und Überlastung. Das erhöht die Nutzungsdauer teurer Komponenten und vermeidet Investitionen in neue Anlagen.
3. Reduzierter Wartungsaufwand
Statt routinemäßig jedes Lager oder jede Dichtung zu prüfen, werden nur die Bauteile gewartet, die tatsächlich Auffälligkeiten zeigen. Das spart Ressourcen, Zeit und Personal.
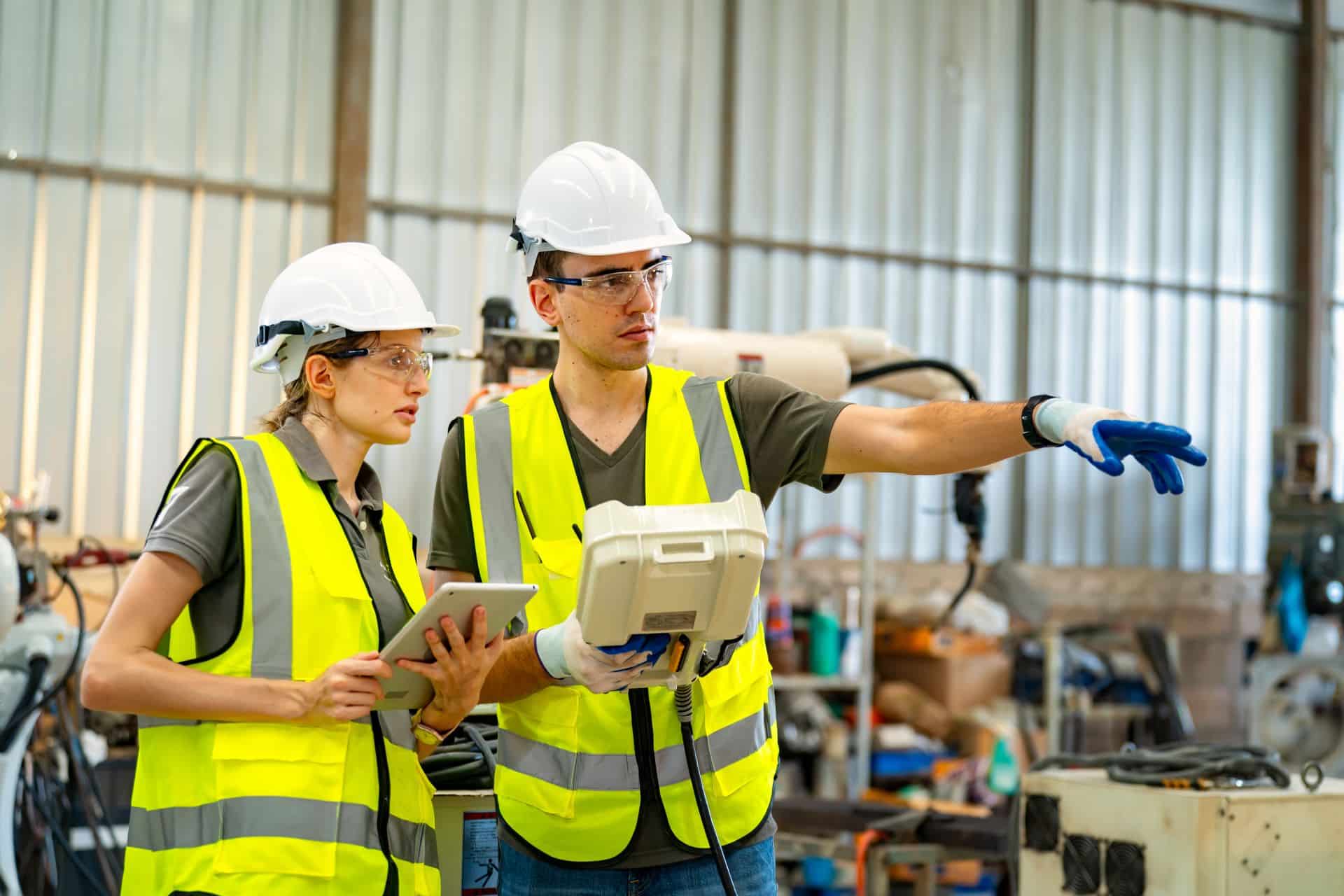
4. Höhere Produktionssicherheit
Mit vorausschauender Wartung wird die Planung zuverlässiger. Produktionsprozesse laufen stabiler, Engpässe durch Ausfälle oder Ersatzteilmangel werden vermieden.
5. Bessere Datenbasis für Entscheidungen
Predictive Maintenance liefert präzise Daten über die Performance von Maschinen – und damit eine Grundlage für strategische Entscheidungen in Instandhaltung, Einkauf und Produktion.
Vorteil | Wirkung in der Praxis |
---|---|
Früherkennung von Problemen | Weniger Notfälle, planbare Wartung |
Ressourceneffizienz | Keine unnötigen Wartungsintervalle mehr |
Transparenz über Anlagenzustand | Genaue Einschätzung des Verschleißgrads |
Verbesserte Ersatzteillogistik | Nur bestellen, was wirklich gebraucht wird |
Nachweisbare Kostenreduktion | Weniger Ausfall, weniger Personalbindung |
Typische Einsatzbereiche für Predictive Maintenance
Predictive Maintenance entfaltet sein Potenzial überall dort, wo Stillstände teuer sind, Wartung planbar sein muss und technische Systeme komplex oder schwer zugänglich sind. Die Einsatzfelder reichen weit über klassische Produktionsumgebungen hinaus.
Industrie & Maschinenbau
-
Fertigungsanlagen, z. B. Pressen, CNC-Maschinen, Roboterarme
-
Fördertechnik, etwa Kettenförderer, Rollenbahnen, Hebesysteme
-
Kompressoren, Pumpen und Ventile – besonders in der Prozessindustrie
Gerade in industriellen Umgebungen zeigt sich, wie wirkungsvoll eine KI-gestützte Zustandsüberwachung sein kann – vor allem, wenn sie flexibel auf verschiedene Einsatzfelder anpassbar ist. Praxisnahe Anwendungsbeispiele zeigen, wie Predictive-Maintenance-Lösungen konkret eingesetzt werden können.
Energieversorgung
-
Windkraft- und Solaranlagen, bei denen Wartungseinsätze teuer und wetterabhängig sind
-
Transformatoren und Generatoren im Netzbetrieb
-
Kraftwerke, z. B. zur Analyse von Turbinen und Dampfleitungen
Transport und Logistik
-
Züge und Güterwagen, etwa für Achslager oder Bremssysteme
-
Flugzeuge, z. B. für Triebwerksüberwachung in Echtzeit
-
LKW-Flotten, für Motor- und Bremsanalytik zur optimalen Wartungsplanung
Gebäudetechnik & Smart Building
-
Aufzugsanlagen, zur Erkennung mechanischer Abnutzung
-
Klimaanlagen und Heizungssysteme, um Energieverluste zu vermeiden
-
Brandschutztechnik, z. B. Lüfter, Türen oder Notbeleuchtung
Landwirtschaft & mobile Maschinen
-
Traktoren, Mähdrescher, Erntemaschinen – oft mit Telemetrie und GPS vernetzt
-
Bewässerungssysteme und Pumpen, insbesondere in sensiblen Klimazonen
Predictive Maintenance in der Praxis: Ein Beispiel aus der Industrie
Theorie ist gut, Praxis ist entscheidend. Ein mittelständischer Automobilzulieferer zeigt, wie Predictive Maintenance konkret umgesetzt werden kann – und welchen Effekt es hat.
Ausgangslage
In der Fertigung kommen mehrere CNC-Fräszentren zum Einsatz. Immer wieder kam es zu ungeplanten Ausfällen, meist verursacht durch verschlissene Spindellager. Die Folge: Produktionsstopps, Lieferverzögerungen und hoher Aufwand für Expressreparaturen.
Umstellung auf Predictive Maintenance
Der Betrieb entschied sich, die kritischen Maschinen mit Vibrationssensoren und Temperatursensorik auszustatten. Die Daten wurden in eine IoT-Plattform eingespeist und mit historischen Betriebsdaten abgeglichen. Ziel war es, auffällige Muster frühzeitig zu erkennen – etwa ungewöhnliche Schwingungsverläufe, die auf Lagerschäden hindeuten.
Ergebnis nach 6 Monaten
Die Einführung der Predictive-Maintenance-Lösung zeigte schnell Wirkung:
-
30 % weniger ungeplante Stillstände
-
20 % geringerer Wartungsaufwand
-
+15 % Maschinenverfügbarkeit
-
Bessere Planbarkeit von Serviceeinsätzen
-
Reduzierung der Ersatzteilkosten durch bedarfsgerechte Bevorratung
Die Verantwortlichen berichten: „Früher mussten wir raten, heute wissen wir – und handeln gezielt.“
Typische Einsatzbereiche für Predictive Maintenance
Predictive Maintenance entfaltet sein Potenzial überall dort, wo Stillstände teuer sind, Wartung planbar sein muss und technische Systeme komplex oder schwer zugänglich sind. Die Einsatzfelder reichen weit über klassische Produktionsumgebungen hinaus.
Industrie & Maschinenbau
-
Fertigungsanlagen, z. B. Pressen, CNC-Maschinen, Roboterarme
-
Fördertechnik, etwa Kettenförderer, Rollenbahnen, Hebesysteme
-
Kompressoren, Pumpen und Ventile – besonders in der Prozessindustrie
Energieversorgung
-
Windkraft- und Solaranlagen, bei denen Wartungseinsätze teuer und wetterabhängig sind
-
Transformatoren und Generatoren im Netzbetrieb
-
Kraftwerke, z. B. zur Analyse von Turbinen und Dampfleitungen
Transport und Logistik
-
Züge und Güterwagen, etwa für Achslager oder Bremssysteme
-
Flugzeuge, z. B. für Triebwerksüberwachung in Echtzeit
-
LKW-Flotten, für Motor- und Bremsanalytik zur optimalen Wartungsplanung
Gebäudetechnik & Smart Building
-
Aufzugsanlagen, zur Erkennung mechanischer Abnutzung
-
Klimaanlagen und Heizungssysteme, um Energieverluste zu vermeiden
-
Brandschutztechnik, z. B. Lüfter, Türen oder Notbeleuchtung
Landwirtschaft & mobile Maschinen
-
Traktoren, Mähdrescher, Erntemaschinen – oft mit Telemetrie und GPS vernetzt
-
Bewässerungssysteme und Pumpen, insbesondere in sensiblen Klimazonen
Technische Voraussetzungen und Systemaufbau
Predictive Maintenance ist keine Plug-and-Play-Lösung. Damit die Systeme verlässlich funktionieren, müssen Technik, Dateninfrastruktur und Organisation aufeinander abgestimmt sein.
Sensorik als Datengrundlage
Herzstück jeder PdM-Lösung sind Sensoren, die direkt an den Maschinen angebracht werden. Je nach Anwendung kommen unterschiedliche Typen zum Einsatz:
-
Beschleunigungssensoren zur Vibrationsanalyse
-
Temperaturfühler an Lagern, Motoren oder Getrieben
-
Druck- und Durchflusssensoren in hydraulischen oder pneumatischen Systemen
-
Strom- und Spannungssensoren zur Analyse des Energieverbrauchs
-
Akustik- und Ultraschallsensoren bei beweglichen Bauteilen
Je präziser und lückenloser die Erfassung, desto besser arbeitet das System.
Datenverarbeitung: Edge vs. Cloud
Die erfassten Daten werden entweder:
-
direkt an eine Cloud-Plattform übertragen, etwa AWS, Azure oder Siemens MindSphere,
-
oder lokal auf Edge Devices vorverarbeitet – ideal bei hohem Datenvolumen oder Echtzeitanforderungen.
In vielen Fällen empfiehlt sich eine Hybridarchitektur, bei der sensible oder zeitkritische Analysen lokal laufen, während Langzeitdaten in der Cloud archiviert und ausgewertet werden.
Analysetools und Prognosemodelle
Je nach Komplexität kommen verschiedene Tools zum Einsatz:
-
Regelbasierte Systeme für einfache Schwellenwertanalysen
-
Statistische Modelle zur Mustererkennung und Trendanalyse
-
Machine Learning / KI-Modelle für lernfähige, dynamische Prognosen
Die Wahl hängt vom Anwendungsfall, Datenumfang und der benötigten Präzision ab.
Integration in bestehende Systeme
Ein funktionierendes Predictive-Maintenance-System sollte an zentrale IT-Systeme angebunden werden:
-
ERP-Systeme (z. B. SAP) – für Instandhaltungsplanung und Ersatzteilmanagement
-
MES-Systeme – zur Rückkopplung an die Produktion
-
CMMS-Software – für Wartungstermine, Benachrichtigungen und Dokumentation
Nur wenn diese Systeme miteinander kommunizieren, entsteht ein echter Mehrwert.
Predictive Maintenance mit KI: Was moderne Systeme heute leisten
Predictive Maintenance ist längst mehr als ein Sensor-Alarm bei Grenzwertüberschreitung. Die wahren Stärken entfaltet das System erst, wenn Künstliche Intelligenz (KI) ins Spiel kommt. Denn Verschleiß kündigt sich oft nicht mit einem einzelnen Messwert an, sondern durch komplexe Muster und subtile Abweichungen.
Machine Learning erkennt, was Menschen übersehen
Algorithmen analysieren historische und aktuelle Datenströme, vergleichen Zustände, erkennen Trends und lernen dazu. Typische Aufgaben:
-
Anomalie-Erkennung: Das System bemerkt untypisches Verhalten – etwa eine ungewöhnliche Vibration bei gleichbleibender Last.
-
Failure Prediction: Es berechnet Wahrscheinlichkeiten für bestimmte Fehler in definierten Zeiträumen.
-
Ursachenanalyse (Root Cause Analysis): KI kann Rückschlüsse ziehen, warum es zu Problemen kommt – oft auf Basis tausender Datenpunkte.
Je größer die Datenbasis und je besser das Training, desto zuverlässiger die Prognosen.
Deep Learning bei komplexen Systemen
In Bereichen mit vielen Einflussfaktoren – etwa bei Triebwerken oder industriellen Großanlagen – kommen Deep-Learning-Modelle zum Einsatz. Sie sind in der Lage, nichtlineare Zusammenhänge zu erkennen, selbstständig Gewichtungen zu setzen und sich an neue Maschinenzustände anzupassen.
Beispiel: Ein neuronales Netz erkennt, dass bestimmte Temperaturschwankungen im Zusammenspiel mit leicht erhöhtem Stromverbrauch auf einen schleichenden Lagerschaden hinweisen – lange bevor ein Alarm ausgelöst worden wäre.
Vorteil: Vorausschau wird zur Empfehlung
Moderne KI-gestützte PdM-Systeme liefern nicht nur „Warnung bei Anomalie“, sondern konkrete Handlungsempfehlungen:
-
„Bauteil X in Maschine Y wird voraussichtlich in 12 Tagen ausfallen. Geplanter Austausch empfohlen.“
-
„Bitte prüfen Sie Schmierungssystem Z – Hinweise auf Unterversorgung.“
So wird Predictive Maintenance zur prescriptive Maintenance – zur intelligenten Assistenz, die Wartung nicht nur voraussagt, sondern aktiv unterstützt.
Wann lohnt sich Predictive Maintenance wirklich?
Predictive Maintenance verspricht viel – doch lohnt sich die Investition für jedes Unternehmen? Die Antwort hängt vom individuellen Setup ab. Entscheidend sind Kostenstruktur, Ausfallrisiken und Wartungsbedarf.
Predictive Maintenance lohnt sich besonders bei:
-
hohen Maschinenkosten – je teurer das Gerät, desto stärker wirkt sich frühzeitige Wartung aus
-
schwer zugänglichen Anlagen – z. B. Windkraftanlagen, Offshore-Technik, Industriepressen
-
kritischen Prozessen – wenn ein Ausfall ganze Produktionslinien lahmlegt
-
schwankenden Belastungen – z. B. bei variablen Schichtplänen oder saisonalen Spitzen
-
komplexen Systemen – mit vielen Einflussfaktoren, die schwer manuell zu überwachen sind
Wirtschaftliche Kennzahlen
Eine erfolgreiche PdM-Einführung lässt sich anhand harter Zahlen belegen:
KPI | Wirkung von PdM |
---|---|
MTBF (Mean Time Between Failures) | steigt – Ausfallhäufigkeit sinkt |
MTTR (Mean Time To Repair) | sinkt – Wartung wird zielgerichteter |
TCO (Total Cost of Ownership) | reduziert sich durch verlängerte Lebensdauer |
ROI | oft innerhalb von 12–24 Monaten erreichbar |
Unternehmen, die eine Pilotphase starten, sollten den ROI klar definieren: Wie viele Ausfälle wurden vermieden? Wie viel Instandhaltungszeit wurde eingespart? Wie haben sich Ersatzteilkosten verändert?
Beispielrechnung (vereinfacht)
-
Produktionsausfall: 10.000 € pro Stunde
-
Vermeidung von 2 Ausfällen à 3 Stunden pro Jahr
-
Einmalige PdM-Einführungskosten: 40.000 €
-
Laufende Systemkosten pro Jahr: 10.000 €
Ersparnis im ersten Jahr:
2 Ausfälle × 3 h × 10.000 € = 60.000 €
→ Abzüglich 50.000 € Kosten = 10.000 € Gewinn im 1. Jahr
In den Folgejahren steigt der Gewinn deutlich – da die einmalige Investition bereits getätigt wurde.
Anbieter und Tools im Überblick
Wer Predictive Maintenance einführen will, hat die Wahl zwischen spezialisierten Softwarelösungen, integrierten Industrieplattformen und branchenspezifischen Systemen. Wichtig ist: Die Lösung muss zur bestehenden Infrastruktur und zum Reifegrad des Unternehmens passen.
Marktführer und spezialisierte Anbieter
Anbieter | Besonderheiten |
---|---|
Siemens MindSphere | Offene IoT-Plattform, ideal für Industrie 4.0-Umgebungen |
IBM Maximo Application Suite | KI-gestützte Analyse, starke Wartungsplanung |
PTC ThingWorx | Fokus auf Industrial IoT, inklusive AR-Integration |
SAP Predictive Asset Insights | Nahtlose ERP-Anbindung, gute Skalierbarkeit |
Bosch IoT Suite | Modular aufgebaut, stark im Maschinenbau und Automotive |
GE Digital Predix | Besonders im Energiebereich etabliert |
Diese Lösungen bieten meist:
-
Datenanbindung via IoT-Gateways oder Edge Devices
-
Visualisierung von Zustandsdaten
-
ML-Modelle zur Ausfallprognose
-
Schnittstellen zu ERP, MES oder CMMS-Systemen
Wichtige Auswahlkriterien
Bevor du dich für eine Plattform entscheidest, prüfe folgende Punkte:
-
Kompatibilität mit bestehenden Maschinen und IT-Systemen
-
Skalierbarkeit – auch für zukünftige Anlagen oder neue Standorte
-
Transparenz – wer hat Zugriff auf welche Daten?
-
Modularität – können einzelne Funktionen separat genutzt werden?
-
Support und Weiterentwicklung – wie aktiv wird das System gepflegt?
Tipp: Starte mit einem Anbieter, der Pilotprojekte unterstützt – viele Plattformen bieten Proof-of-Concept-Pakete mit fixen Laufzeiten und klaren Zielen.
5 Umsetzungstipps für den Einstieg in Predictive Maintenance
Der Einstieg in Predictive Maintenance muss kein Großprojekt sein – vorausgesetzt, er ist gut vorbereitet. Wer schrittweise vorgeht und von Anfang an klare Ziele definiert, kann schnell Erfolge messen.
1. Klein anfangen, gezielt skalieren
Starte mit einer Pilotmaschine, die häufig ausfällt oder besonders wichtig ist. So lassen sich Technologie, Prozesse und Verantwortlichkeiten im überschaubaren Rahmen testen. Erst danach erfolgt die skalierte Einführung im gesamten Betrieb.
2. Relevante Use Cases definieren
Nicht jede Maschine braucht Predictive Maintenance. Konzentriere dich auf:
-
kritische Anlagen
-
Systeme mit hohem Wartungsaufwand
-
teure oder schwer zugängliche Bauteile
Daten um der Daten willen bringen nichts – entscheidend ist der konkrete Nutzen.
3. Datenstrategie aufbauen
Frage dich:
-
Welche Daten fallen bereits an?
-
Welche Sensoren fehlen noch?
-
Wo werden Daten gespeichert?
-
Wer hat Zugriff und wer interpretiert sie?
Ohne strukturierte Datenstrategie bleibt Predictive Maintenance ein theoretisches Konzept.
4. Schnittstellen sichern
Predictive Maintenance entfaltet erst dann vollen Nutzen, wenn alle Systeme miteinander kommunizieren. Sorge für saubere Schnittstellen zu:
-
ERP (z. B. SAP)
-
MES (Produktionssteuerung)
-
CMMS (Wartungsmanagement)
Vermeide Datensilos – und sorge für klare Zuständigkeiten.
5. Akzeptanz im Team schaffen
Technologie allein reicht nicht. Nur wenn Techniker, Instandhalter und Führungskräfte den Nutzen verstehen, wird das System angenommen. Schulungen, Erfolgsmessungen und offene Kommunikation sind entscheidend.
Fazit: Predictive Maintenance ist kein Trend – es ist eine Strategie
Predictive Maintenance verändert, wie Unternehmen auf technische Risiken reagieren. Statt auf Ausfälle zu warten oder starr nach Plan zu handeln, erlaubt der datenbasierte Ansatz präzise Eingriffe genau zum richtigen Zeitpunkt. Die Technik ist da, die Lösungen sind ausgereift – was zählt, ist ein strukturierter Einstieg und die Bereitschaft, Maschinen nicht länger als Black Box zu behandeln.
Wer frühzeitig investiert, profitiert von weniger Ausfällen, besserer Planbarkeit und einem klaren Wettbewerbsvorteil. Predictive Maintenance ist nicht nur eine Option – sondern eine logische Antwort auf die Anforderungen moderner Industrieprozesse.
Bildnachweis:
WMSTUDIO – stock.adobe.com
metamorworks – stock.adobe.com
FotoArtist – stock.adobe.com
WahdaniSafri – stock.adobe.com